Обычного держателя банковской карты вопросы комиссий, тарифов и остатка на счете явно волнуют больше, чем тонкости производства этого кусочка пластика. Между тем процесс этот интересен, высокотехнологичен и максимально строго охраняем. Тем более любопытно обозревателю Банки.ру было посетить один из подмосковных заводов и увидеть, как делаются банковские карты.
Под присмотром Большого Брата
В принципе услуги по изготовлению обычных пластиковых карточек предлагаются чуть ли не на каждом шагу. Интернет пестрит объявлениями компаний, готовых в минимальные сроки выпустить едва ли не любой тираж карт различного назначения и сложности. Действительно, у таких изготовителей можно заказать определенное количество дисконтных, бонусных, клубных карт или подарочных сертификатов. Но банков среди их клиентов нет. Потому что банковский пластик — это не просто карта.
Как известно, львиная доля обращающихся на российском рынке банковских карт относится к международным платежным системам Visa и MasterCard. И эти компании имеют очень строгие требования к производителям пластика — каждое предприятие, собирающееся выпускать банковские карты, должно пройти специальную сертификацию. Таких заводов в России не много: «НоваКард», «Розан Файнэнс», «Орга Зеленоград», «Ситроникс», «Гознак». Недавно на рынке производства пластика появился новый игрок — входящий в холдинг ITG завод «Алиот», который и посетила автор этой статьи.
Требования Visa и MasterCard к физической безопасности производства очень жесткие. По словам директора по общим вопросам «Алиота» Игоря Краснова, их перечень — это «серьезные талмуды», и необходимо неукоснительно следовать каждой строчке. На территории предприятия установлено 60 камер теленаблюдения, и только шесть из них — внешние. Остальные являются всевидящим оком, из пристального внимания которого не выпадет ни один сотрудник завода. «Мы гарантируем, что наши продукты не пойдут по криминальным каналам», — подчеркивает Краснов.
Шлюз для прохода сотрудников на территорию производственных помещений контролирует вес входящего (максимум 110 кг), что должно исключать возможность проникновения по одному электронному ключу сразу двух человек. В противном случае приятный женский голос напомнит, что в шлюзе должен находиться только один человек. Очевидно, что слишком тучным гражданам в работе на данном предприятии отказывают — или предлагают сначала похудеть хотя бы до указанного максимума.
В производственных помещениях — как в лабораториях: просторно, светло, тихо и безлюдно. Из соображений безопасности за работой в цехах можно понаблюдать только через большие стеклянные окна. В каком-то помещении один работник, в каком-то — два или три, не больше. Кстати, работники из одного цеха не могут контактировать с коллегами из другого — таковы правила по всему заводу. Поэтому между цехами тоже существуют шлюзы. Пока дверь шлюза открыта на стороне одного помещения, на стороне другого ее открыть невозможно.
Пластик пластику рознь
По словам Краснова, пластиковые карты выпускаются разные. Есть из поликарбоната — карточки получаются более толстыми, твердыми и негнущимися: на их основе делают документы, например водительские права. Такой продукт достаточно дорогой. Есть четырехслойные — тонкие, прочные и гибкие. Как раз такие карты делают для банков (это карты любого класса — от Mass и Electron до Gold или Platinum) и многих небанковских программ лояльности. Обычные дисконтные карточки иногда бывают попроще и подешевле. Но основной продукт, как отметил Краснов, — это четырехслойный пластик.
На данный момент большинство заказов на «Алиоте» — это дисконтные карты: для компаний «ЛЭтуаль», «РОСНО», «Эльдорадо», «Доктор Столетов» и других. Из банков заказчиком пока является Бинбанк, но уже ведутся переговоры и с другими кредитными организациями — сертификацию в Visa и MasterCard завод получил недавно.
Если говорить о самом сырье, то, по словам Краснова, в России материал для карт не производят. «Крупнейшие производители — это компании в Германии и Италии, — рассказал он. — Мы работаем с немецким пластиком. Еще в Китае делают, но он как-то… не очень».
Метаморфозы
В печатном цехе, который является первым в технологической цепочке производства карт, работают офсетная и трафаретная машины, нанося требуемые для карт изображения на тонкие листы пластика. На черном фоне вышедшего из машины тонкого пластикового листа было написано название крупной сети магазинов одежды из кожи и меха. По всей видимости, пора готовиться к весенним распродажам…
Листы с печатью отправляются в другой цех — ламинации. Там собираются своеобразные четырехслойные «сэндвичи» из окрашенных листов и листов ламината. «Сэндвичи» запекаются в единое целое и отправляются (опять-таки через шлюз) в цех вырубки. Что происходит там — понятно. Специальные машины вырубают из листов карточки привычного нам вида и размера (ширина — 86 мм, высота — 54 мм, толщина — 0,76 мм). Из одного листа получается 24 карты. Там же на пластик наносятся голограммы и полосы для клиентской подписи.
Отходы после вырубки тоже не должны пропадать — это высококачественный немецкий поливинилхлорид, который можно измельчить, расплавить и пустить на отливку, например, сантехнических труб. По словам Краснова, как раз сейчас ведутся переговоры о продаже отходов производителям пластиковой сантехники. Туда же планируется направлять и бракованные карты. Правда, их количество невелико — около 1% от общего объема продукции.
После вырубки карты уже имеют вполне приличный вид. Не хватает им одного — «мозгов». Для того чтобы кусочки блестящего пластика стали полностью функциональными, их отправляют в самое сердце завода — цех имплантации. Две умные и очень дорогие немецкие машины под руководством программиста осуществляют персонализацию карт: одна наносит магнитную полосу, вторая вклеивает микрочип. Там же производится эмбоссирование — нанесение выдавленных символов. За процессом наблюдает еще один сотрудник, который при необходимости загружает в имплантационные машины очередную порцию карт. Полоса наносится практически молниеносно, а вот на вклейку одного чипа может потребоваться до 20 секунд.
Если цех имплантации — сердце завода, то сейф — это явно святая святых. В защищенном отдельном помещении площадью 80 кв. м можно хранить до 20 млн готовых карт. Правила допуска туда очень строги: войти в помещение сейфа могут только два человека, и только одновременно. Сотрудники набирают код, одновременно прикладывают свои электронные ключи к считывателям, и только тогда дверь сейфа можно открыть.
Чем больше — тем лучше
Большинство кредитных организаций, опрошенных Банки.ру, заказывают свои карты на предприятии «Розан Файнэнс»: здесь делают пластик для ВТБ 24, Альфа-Банка, Росбанка, «Уралсиба», НБ «Траст», Юниаструм Банка, ЮниКредит Банка, банка «Тинькофф Кредитные Системы», РосЕвроБанка, СМП Банка и многих других. ВТБ 24 также пользуется услугами заводов «Ситроникс», «Гознак» и «НоваКард». На «НоваКарде» изготавливают карты и для Альфа-Банка и ОТП Банка. Пробизнесбанк заказывает свои карты за границей — на заводе TAG Systems в Андорре.
Вместе с тем, по мнению гендиректора «Алиота» Игоря Колесова, российский рынок производства пластиковых карт не перенасыщен и не монополизирован крупными игроками. «Чем больше участников — тем выше конкуренция и, соответственно, более выгодные цены для банков», — подчеркнул он. На первом этапе предприятие планирует выпускать 5 млн карт в месяц, а через два года, когда производственные мощности будут полностью загружены (сейчас занятость цехов — 40—50%), их выпуск будет увеличен до 30 млн карт в месяц. По словам Колесова, стоимость выпуска одной карты для банка зависит от ее вида и тиража и составляет порядка 0,1—1 евро.
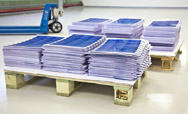
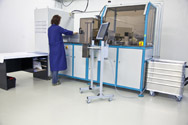
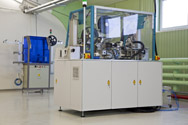
Татьяна ТЕРНОВСКАЯ, Banki.ru